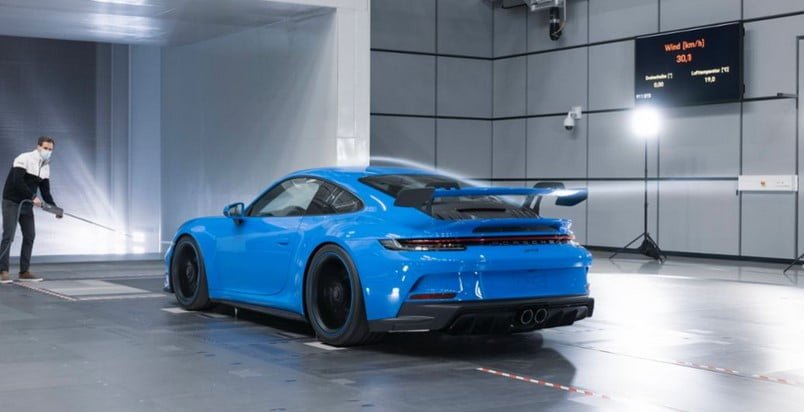
The new Porsche 911 GT3 is packed with technical highlights. During development, engineers pursued a particular goal: to further enhance the performance of the high-performance sports car without compromising daily usability.
The collaboration between series development engineers and specialists from the Motorsport department played an immensely important role here. “When we have the same engineers developing our race cars and also working on the design of a new GT car for the road, that’s the most direct technology transfer I can imagine,” explains Andreas Preuninger, Director of GT Model Line.
Technological progress in the area of aerodynamics is particularly evident. It is the first time a suspended rear wing is installed on a Porsche production car. Its swan-neck mounting is used similarly in the GT 911 RSR race car and the one-make cup race car, 911 GT3 Cup.
As two aluminum supports now hold the wing element from above, the airflow can pass through without disturbance from below, which is aerodynamically more sensitive. This new design led to a reduction in flow losses and not only increased aerodynamic downforce but also resulted in well-balanced negative lift conditions along with many other detailed measures.
“We developed the aerodynamics of the new 911 GT3 in around 700 simulations. We spent over 160 hours fine-tuning the car in the wind tunnel,” explains aerodynamics engineer Mathias Roll.
The angle of attack of the new rear wing can be set in four different positions. Consequently, the front diffuser can also be adjusted in four positions. “The new 911 GT3 generates 50% more aerodynamic downforce than its predecessor at 200 km/h in the factory setting alone. In the maximum aerodynamic downforce setting, the increase is up to over 150 percent,” Roll adds.
Similar to motor racing situations, the aerodynamic balance of the new 911 GT3 can be individually adapted to track conditions and individual driving style. “In our state-of-the-art wind tunnel in Weissach, we not only drive in a straight line; we simulate all imaginable driving situations. We make the car move, pitch, and yaw to simulate physical influences on the track,” explains the aerodynamics engineer.
Regarding the engine, the development of the high-revving, naturally aspirated 4.0-liter engine (911 GT3: combined fuel consumption 13.3 – 12.4 l/100 km, combined CO2 emissions 304 – 283 g/km) required considerable time. “In total, the engine of the new GT3 ran for over 22,000 hours on the test bench. During testing, we repeatedly simulated typical race circuit profiles and ran the engine at full speed for a large portion of the time,” explains Thomas Mader, Project Manager for GT Road Car Engines.
The engine, responsive when the accelerator is pressed, is based on the race car engine from the 911 GT3 R race car and is also used practically unchanged in the 911 GT3 Cup. With 375 kW (510 PS), its power is 10 PS higher than in the predecessor GT3 model. It delivers its maximum power at 8,400 rpm, and the electronic limiter only activates this extraordinary acceleration capability at 9,000 rpm. The maximum torque has been increased from 460 to 470 Nm.
The high longitudinal and lateral acceleration forces produced by the new 911 GT3 on race tracks make the oil supply for the high-revving engine of special importance. As in motorsports, this is done through a dry-sump lubrication system with a separate oil tank.
With a total of seven suction stages, this quickly and efficiently directs the engine oil back to the external tank, while the lubrication of the highly loaded connecting rod bearings is done directly through the oil pump via the crankshaft. “The engine of our 911 GT3 Cup race car essentially differs in two components: the exhaust system and the engine control unit. Everything else is identical,” explains Mader.
The engineers and test drivers also tested the engine of the new 911 GT3 outside of the test bench. “We performed 600 emission tests during development to meet strict standards,” says Thomas Mader. Very strict standards were also applied in terms of engine endurance: it had to function flawlessly in a continuous stretch of over 5,000 kilometers on the Nardo oval in Italy at a constant speed of 300 km/h, stopping only for refueling.